Industrial Explosive Cleaning
Our explosive cleaning process is straightforward and quite simple: foulant and debris are removed through the controlled use of explosives.
Groome is continuously evolving and improving our process as our engineers tap into the latest technology behind explosive cleaning. There are two main methods of explosive cleaning that our team utilizes. Both are safe, simple and effective ways to clean.
Stick / Binary Explosive Cleaning
This method uses two-part binary components that are composed of an ammonium nitrate base and a nitro methane fuel additive. Separate, these ingredients are not explosive, but once mixed this combination is. Denotation requires a blasting cap, which is not introduced until right before the explosive is placed into position.
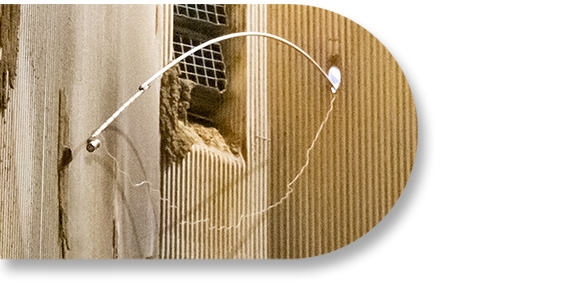
Detonation Cord Explosive Cleaning
Detonation cord, commonly known as det cord, is a thin, flexible plastic tube filled with PETN, a high-explosive that requires a blasting cap for denotation. As part of Groome’s safety standards, the addition of the blasting cap is the last step before detonation protocols begin. Once initiated, the cord detonates at approximately 22,000 ft/sec.
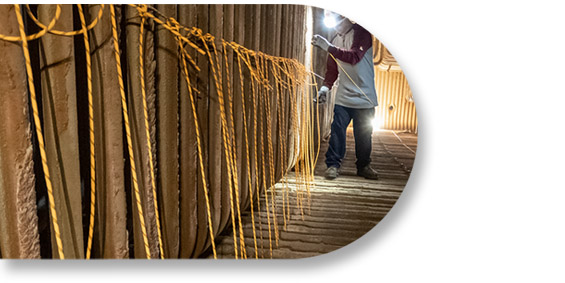
INDUSTRIAL APPLICATIONS
COAL-FIRED POWER PLANTS |
PETROCHEM / REFINERIES |
CONCRETE / MANUFACTURING |
WASTE-TO-ENERGY |
PULP & PAPER |
STEEL / METAL CASTING FOUNDRIES |
TRONA / SODA ASH |
Safety Is Paramount at Groome
We follow IME/OSHA-based safety training programs, along with an OSHA 10 training standard for all employees.
An accident-free environment translates to lower insurance costs, better employee commitment, higher productivity, and an improved bottom line for our customers.